
According to the World Steel Organization, around 50% of the steel produced on Earth ends up in the construction industry. So, when people talk about a metal building, they’re usually referring to one made from steel.
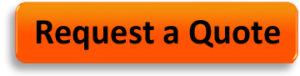
Steel is a versatile, eco-friendly, and durable choice for a wide range of applications, including garages, workshops, agricultural buildings, and sheds.
Contractors use metal for building homes, too, but we’re usually referring to complete steel structures when referring to metal buildings.
If you’re considering buying a metal structure, keep reading to find out more about the factors that can affect their price.
What Are Metal Buildings Used For?
You can use a metal building for almost anything, but they’re most popular for the following applications:
- Guard houses
- Farm buildings
- Equestrian barns and arenas
- Garden sheds
- Metal garage buildings
- Warehouses
- Schools
- Sports Facilities
- Airplane hangars
Steel buildings are available in a range of sizes to suit these applications, ranging from 8′ x 20′ to 24′ x 56′ and more.
Metal Buildings Cost Considerations
According to the NAHB, steel prices have stabilized after huge increases during the pandemic, while most other building materials are around 19% more expensive than they were last year.
That doesn’t mean steel is cheaper per square foot than other materials, like wood. Yet, the overall cost of constructing your building often works out cheaper when you choose steel.
Steel has much greater tensile strength than other building materials, so you’ll use less of it during your design. A steel building doesn’t require extensive foundations either, further decreasing the building costs.
If you’re building a steel building from scratch, daily fluctuations in supply and demand will impact the cost of your building. While this doesn’t impact prefabricated metal building kits, it can affect the availability of these buildings.
Apart from the current price of steel, five factors can impact the price of metal buildings.
The Type of Metal
Metals occur widely in construction. Builders use them for a huge range of things including rebar, windows, roofing, plumbing, and heating equipment.
Regarding exteriors, there are four common types of metals used:
- Stainless steel with a chromium oxide coating
- Brass, copper, and bronze for ornamentation
- Aluminum is cheaper and lightweight
- Galvanized steel coated with liquid zinc for extra corrosion resistance
Stainless steel is the strongest of these materials, but also the most expensive and offers no protection against corrosion. For this reason, it’s the first choice for building modular steel buildings.
Building Design
The bigger the building, the higher the cost to purchase it.
Not only does the size of your building impact the raw materials, required, but it also affects the labor costs associated with constructing it. It takes longer to erect a bigger building with more customizations and features.
Modular steel buildings involve the lowest labor costs for the client, as it’s easy and quick for workers to erect these buildings on site.
The height, width, length, and roof pitch of your building all impact the costs in different ways. For instance, making your building longer to increase its square footage is cheaper than widening it.
That’s because you’ll need extra reinforcement to cope with additional width.
Fuel Costs
Fuel prices can affect the price of steel buildings in two ways. Firstly, the price of fuel impacts the cost of transporting steel to the manufacturer’s warehouse, and secondly, it increases the cost to deliver the building to your construction site.
The Supplier
Large, established manufacturers and cooperatives can afford to buy steel in bulk. This means they get better prices at the outset and results in lower costs for the client.
Your Location
Where you live has a major impact on the cost to erect a metal building. For starters, permitting costs will add to the overall expenses, and the local climate impacts the design of your building.
The following factors can influence the cost of your building depending on where you live:
The Weather
For safety’s sake, and to comply with building codes, you’ll need to choose a building with a high wind rating if you live in one of the states that experience high winds or hurricanes.
That means you’ll pay extra costs associated with engineering the building to stand up to these conditions.
You can’t build a metal building with open sides in these areas, either. Open sides don’t afford as much protection against up-drafts, so you’ll need to pay for more steel when constructing your building.
In snowy areas, buildings must have a suitable snow rating. The more snow your building must withstand, the stronger and sturdier it needs to be, resulting in higher costs.
Seismic Conditions
If you live in an area that’s prone to earthquakes, it’s essential to reinforce your building against these incidents. In areas with high seismic ratings, you’ll need to construct specially designed earthquake-proof metal buildings that cost more.
Steel is extremely strong, but it’s also surprisingly flexible. That means it won’t crumble in the event of an earthquake as concrete does.
Earthquake-proof buildings always cost more, but building a steel building that can stand up to earthquakes is cheaper than constructing one from weaker materials.
Local Prices
Labor and material costs vary from place to place. In most cases, places with a high cost of living attract higher labor costs, too.
That’s because employers must pay higher wages if they want to attract qualified, experienced employees.
In remote locations, you can expect to pay higher delivery costs. Most manufacturers have their operations close to arterial routes to facilitate a reliable supply of steel.
What’s more, the components needed to build a metal building arrive on a large truck and trailer. If this vehicle can’t access your property easily, you’ll pay more for transporting smaller loads.
The Costs to Construct a Metal Building
A lot more goes into constructing a metal building than erecting the metal components. Several other costs come into play during the construction process.
So, while you could pay as little as $28,200 for a 40×60 metal building of 2,400 sq ft, you can add at least another $10 to $20 per square foot for the other costs involved. These include:
Constructing a Foundation for Your Steel Building
Unlike conventional structures, metal buildings don’t require deep structural foundations. The steel purloins rest on concrete footings that bear the load of the building.
You will need to level your site and pour a concrete slab to act as a floor for your building. These initial preparations may add up to $7 per square foot to the cost of your building.
Metal Building Customizations
Most modular steel buildings come with standard features like doors and windows. If you want to add extra openings or move their location, you can expect to pay a little more for these customizations.
You can add vehicle entryways, skylights, interior metal partitions, walkways, and attics to a metal building if desired.
Insulation is one final cost consideration when constructing a metal building. This feature can cost between 50 cents and $3 per foot.
Insulation with a higher R-value costs more. Once again, the type of insulation you need will depend on your building’s location.
Remember to factor the cost of the following into your costs, too:
- Lighting
- Electrical points
- Plumbing
- Gutters
- Downpipes
- Ventilation
Dry walling, sanding, and painting interior walls can cost at least $2 per square foot.
Energy-Efficient Features
When you choose a metal building for your business premises, you could benefit from attractive tax incentives. You can enjoy more incentives plus cost-savings on your energy bills if you implement further energy-efficient modifications.
Steel roofs are ideal for installing solar panels, and steel is also an environmentally-friendly choice. It’s recyclable and manufacturers produce few carbon emissions when forging it.
Is it Worth Building a Steel Building?
Steel buildings offer the following benefits for business owners:
- Durability
- Low maintenance
- Many customizations and sizes
- Weather and fire-resistance
- Low insurance costs
- Insect, mold, and mildew resistance
- Fast construction
- Low labor costs
Finally, modular metal buildings offer uniformity of design and consistent quality throughout.
You’ll also have fewer occupational safety worries when you build a modular building. That’s because of the simple, standardized construction process and because most of the work takes place off-site.
Find the Best Prices for Metal Buildings
If you want to achieve the best value for money when erecting a steel building, you must shop around and compare prices before you commit. Prices may vary considerably from supplier to supplier depending on their experience, warranties, and the services they offer.
Comparing the costs of modular metal buildings is the best way to get accurate pricing and decide on the most cost-effective solution for you.
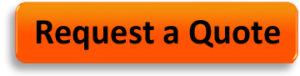